Work Orders
Work Orders
Work orders help track repairs, maintenance tasks, and associated costs for vehicles, stations, and equipment. The FireWorks system provides comprehensive work order management from creation through completion and cost tracking.
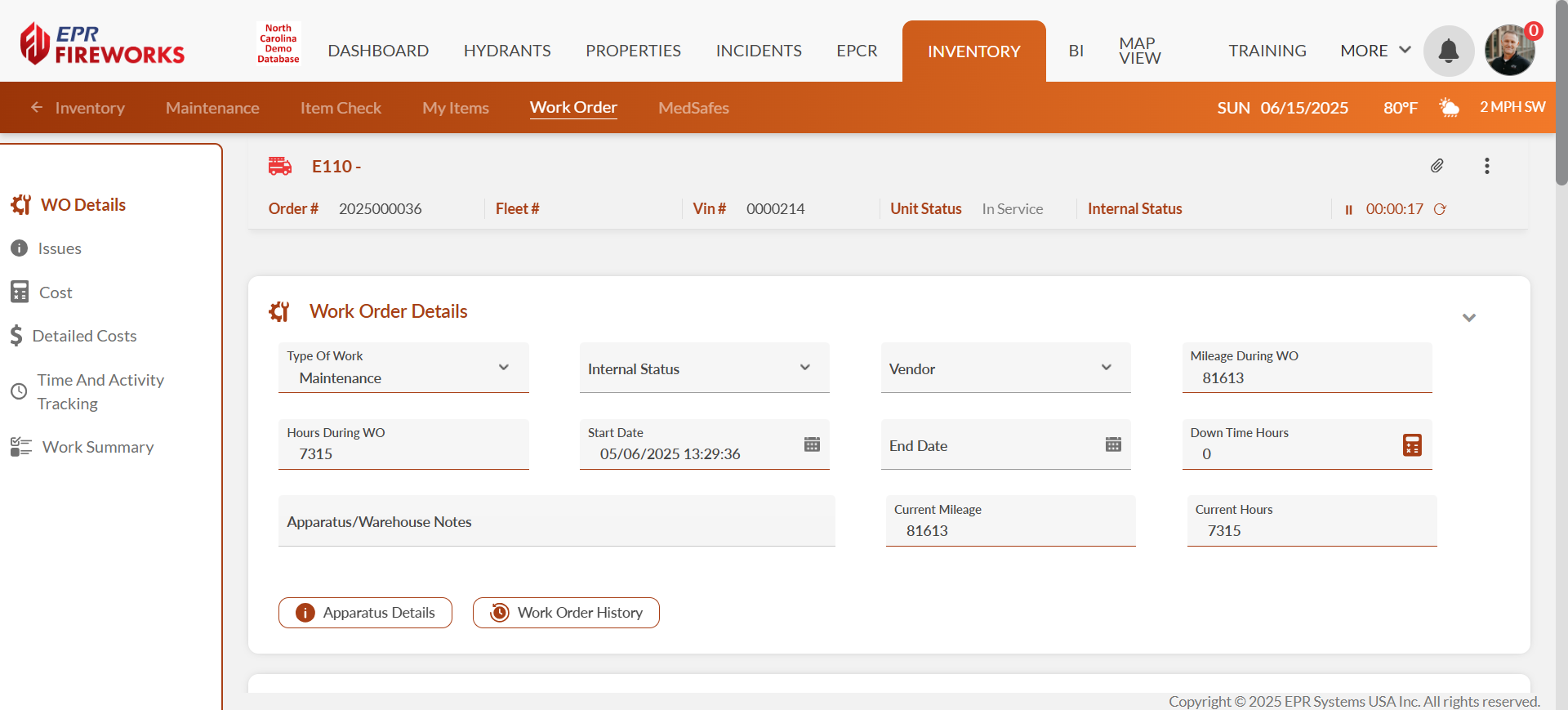
If this is your first time using work orders, review the Work Order Interface Guide to familiarize yourself with the workspace layout.
Work Order Types
Work orders can be created for different object types:
Apparatus/Warehouse - Vehicle and warehouse maintenance
Hydrant - Fire hydrant repairs and maintenance
Item - Equipment repairs and replacements
Station - Station facility maintenance
Work types include fuel, maintenance, parts replacement, and repair tasks.
Work Order Process
Creating Work Orders
Set up new work orders from multiple starting points and configure basic work details including vendors, timelines, and issue documentation.
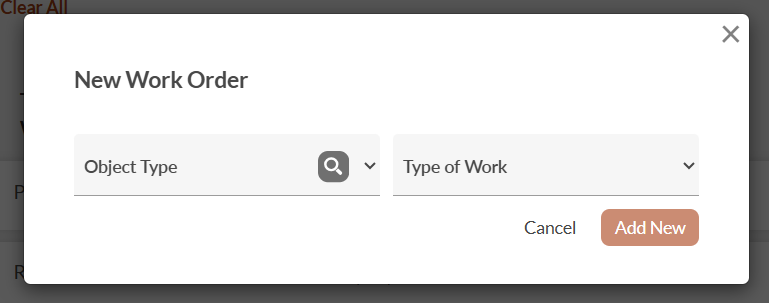
Documenting Work Orders
Track costs, labor, and progress for active work orders through completion with comprehensive documentation and cost management.
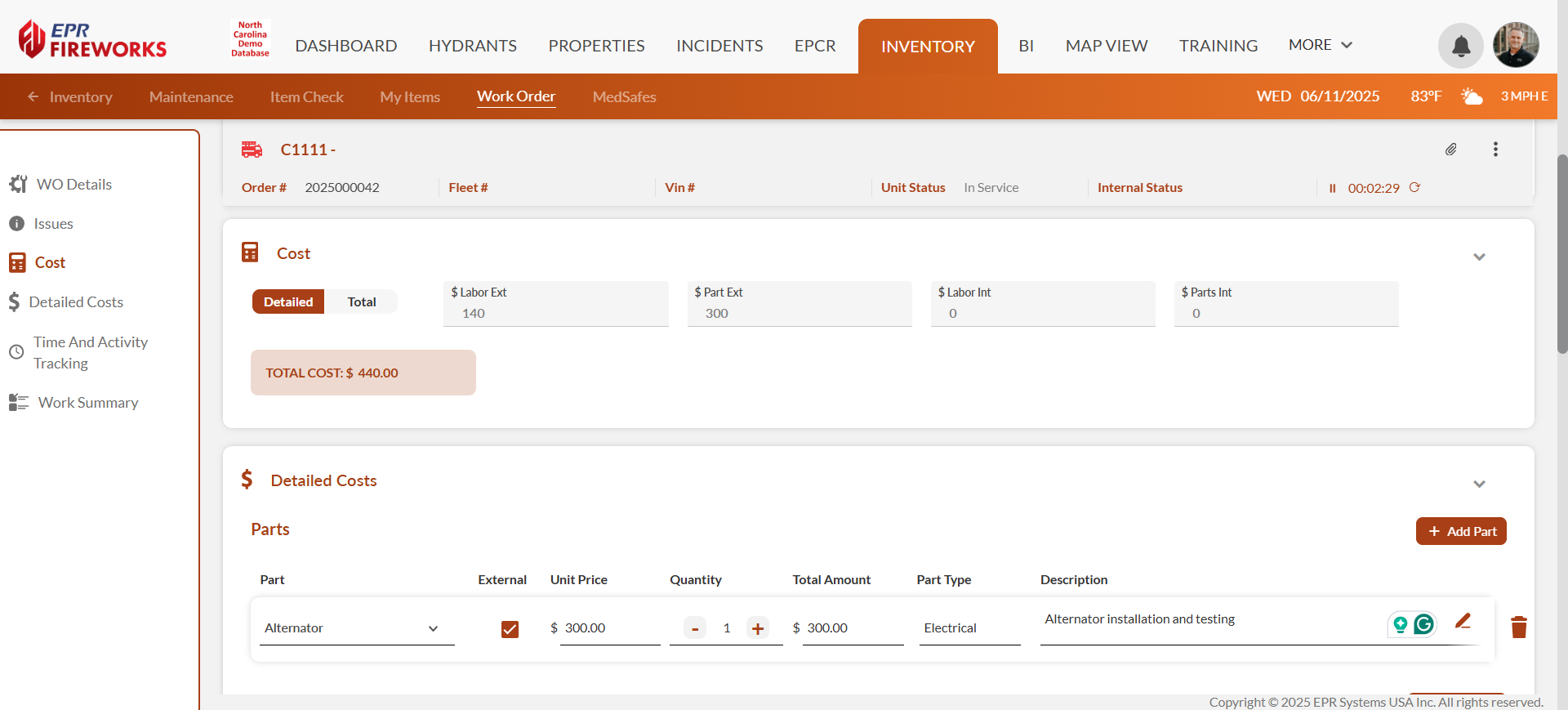
Getting Started
Before creating or managing work orders:
Verify you have appropriate permissions to create and manage work orders
Gather relevant information about the issue or maintenance task
Have vendor information ready if external work is needed
Ensure apparatus, item, or station has unique identifiers in the system
Integration Points
From Maintenance Checks
Work orders automatically generate from maintenance checks when issues are marked as NOT OK. Enable seamless conversion from check findings to actionable work orders.
Cost Tracking Options
Choose between detailed cost tracking (individual parts and labor) or total cost entry for streamlined documentation based on your department's needs.
Time and Activity Tracking
Document real-time or manual time tracking for activities, staff assignments, and duration reporting with built-in timer functionality.