Work Order Interface Guide
Interface Overview
The Work Order interface consolidates all work order management functions into an organized workspace. Understanding the work order interface helps you navigate efficiently and manage maintenance tasks accurately, saving time and ensuring all important repair and maintenance information is properly documented.
The layout consists of a quick-access menu, a key information bar, and a main workspace to manage work orders, track progress, and document completion details efficiently.
This guide describes the Work Order tab GUI. To create or document work orders, see Work Order.
Quick Access Menu
Everything you need is on the left side:
WO Details - View complete work order information.
Issues - Document and track problems found during maintenance.
Cost - Record parts, labor, and total costs.
Detailed Costs - Break down expenses by category.
Time and Activity Tracking - Log hours and activities.
Work Summary - Review completed work and outcomes.
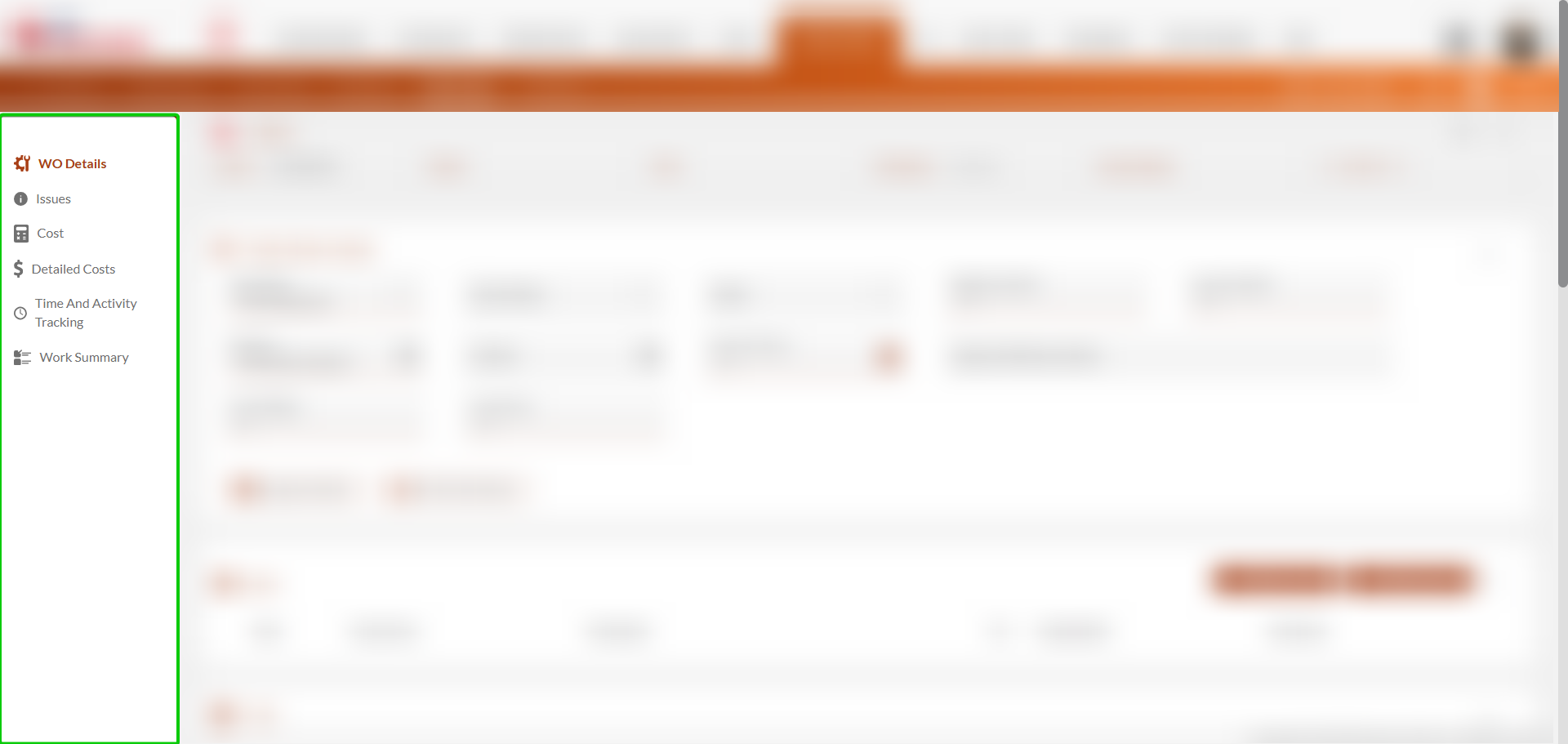
Key Information Bar
At the top, you'll see the essential details at a glance:
Work order number (e.g., C1111-)
Order number
Fleet number
VIN number
Unit status (In Service/Out of Service)
Internal status
Timer showing current work duration
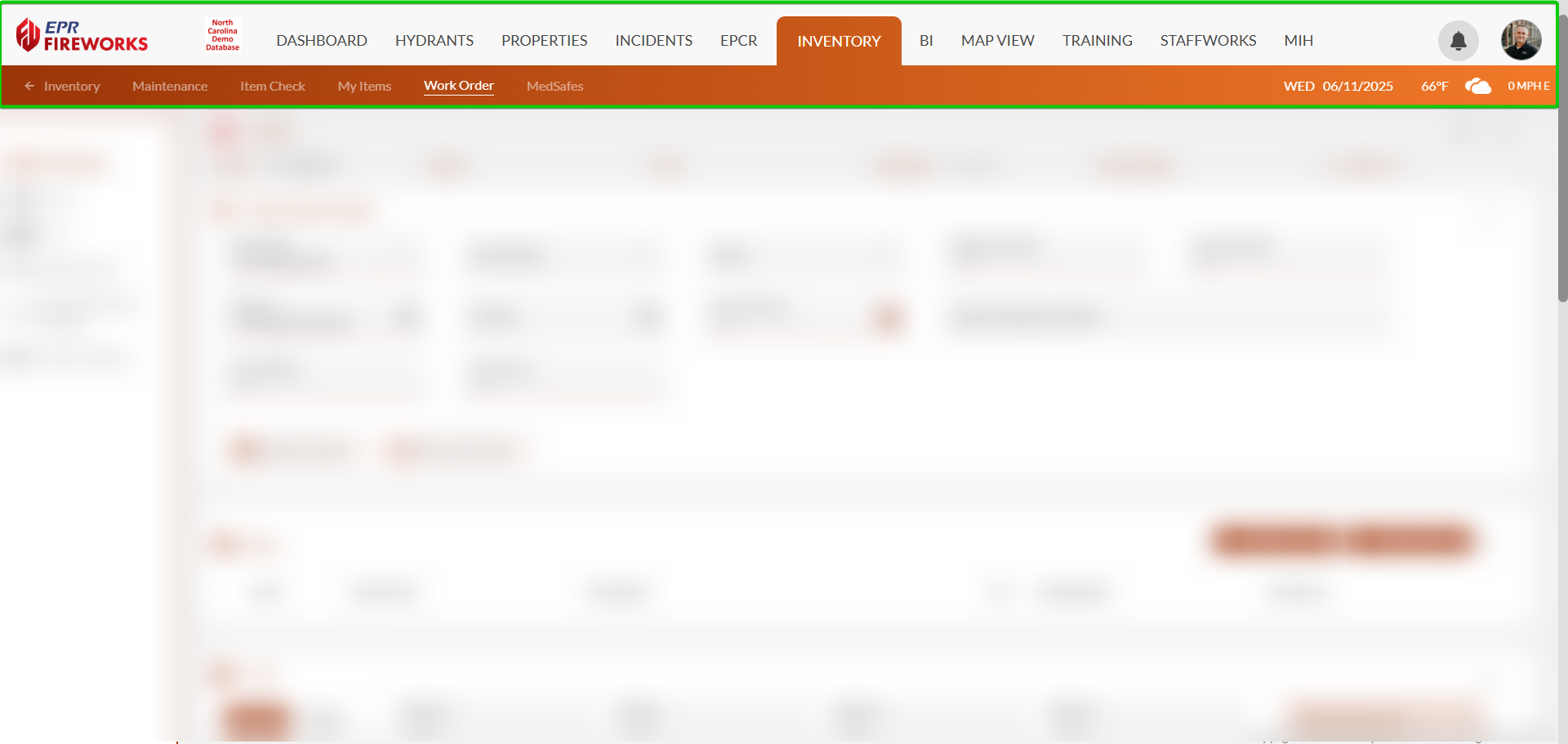
Main Workspace
This is where you'll do most of your work. Here you can:
Configure work order details and track maintenance progress
Document time, mileage, and equipment hours
Record issues found during maintenance work
Track parts, labor, and total maintenance costs
Review work order history and completion status
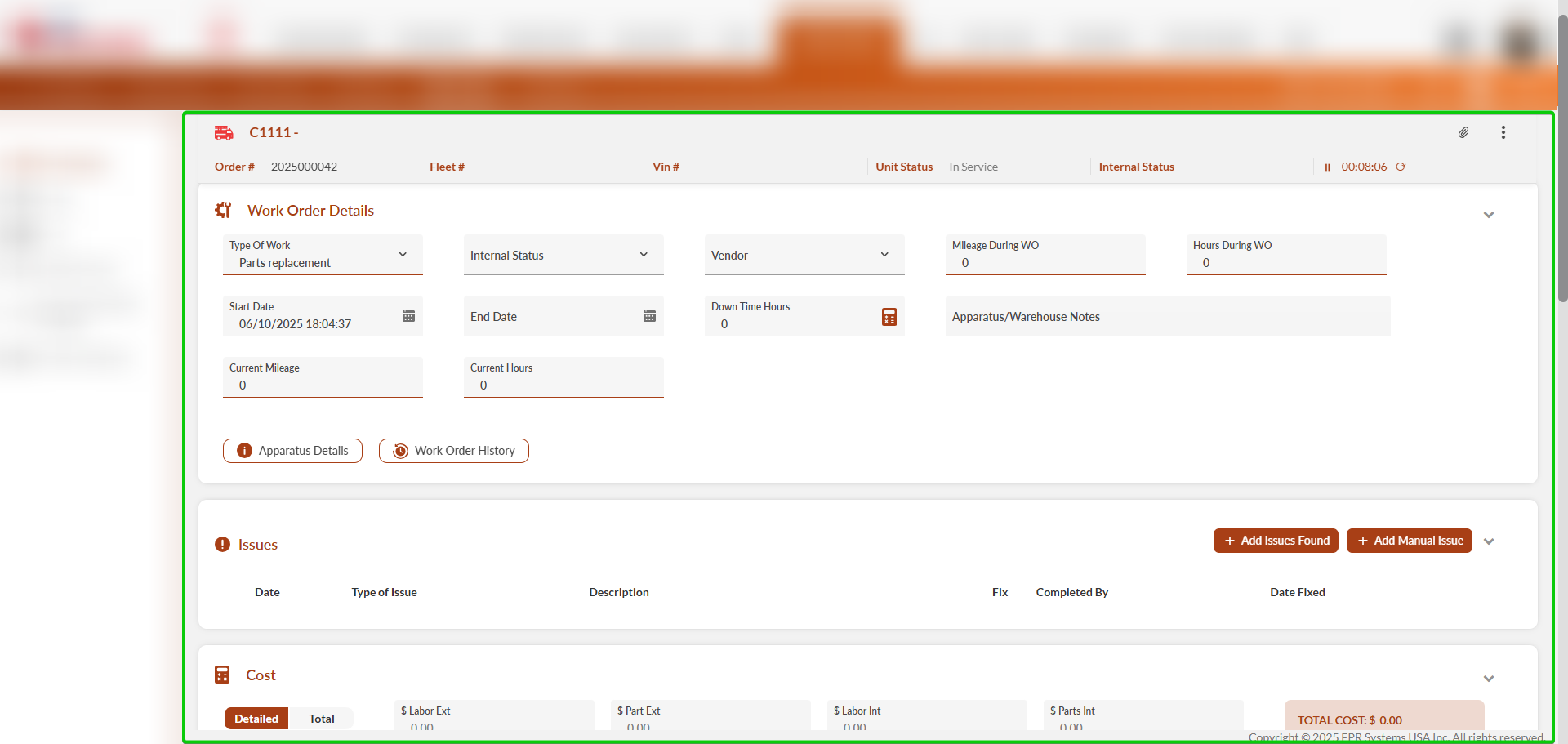
Note: Work order screens may vary based on equipment type and department configuration. The interface adapts to show relevant fields for different maintenance scenarios.