Inventory & Maintenance - Release Notes
May 2025
Inventory & Maintenance > Department Items
We added the Remove from Location button to the Change Location popup in the Department Items table, enabling you to easily remove an item from its location.
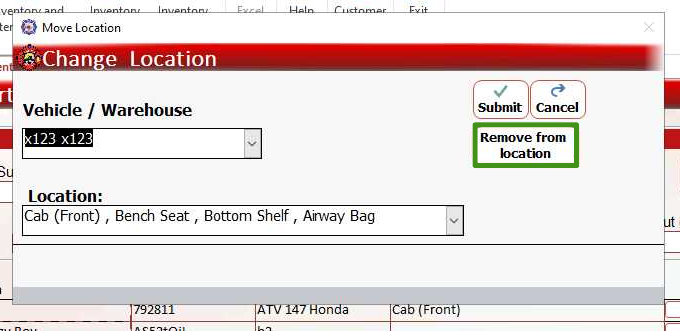
March 2025
Inventory & Maintenance > Maintenance Templates for Item Checks
Create maintenance categories for Item Checks (previously available only for apparatuses) to assign preset check lists to items. Set issues to trigger work order requests when marked NOT OK.
The following procedure describes how to create maintenance categories, add them to items, and enable work order requests for specific issues:
Creating a Maintenance Category
Go to Inventory & Maintenance > Settings > Maintenance Categories.
In Category Type, select Equipment.
Click New.
Enter a name in the Description column.
Add maintenance types in the Add Type of Maintenance field.
Click Exit when finished.
Adding Maintenance Type to Items
Go to Settings > Items.
Double-click the desired item.
Select the Maintenance Check Category tab.
Select your maintenance category from the Add Category dropdown, and then click Add.
Check Work Order to enable work order requests.
When done, click Exit.
January 2025
Merge Items (Follow-Up Items)
You can merge items to avoid duplicates within Items:
In the Follow-Up Items table, click Merge Items.
The Merge Items window will open. Select the duplicates from the dropdown lists, and then click Merge.
Toggling Between Item Locations (Inventory Requirements)
When using the Search Item dropdown list to find a specific item, you can now toggle between its locations within the apparatus or warehouse by clicking the arrows on either side of the item.

Back to all Back-Office releases.