Maintenance Check
Overview
Document your inspections of apparatus and warehouse equipment using maintenance checks on daily, weekly, monthly, quarterly, bi-annual, and annual schedules. This procedure helps you record what you find and report any problems that need fixing.
Note: You can combine maintenance and inventory checks by enabling Include Maintenance Check within the Inventory Check workflow.
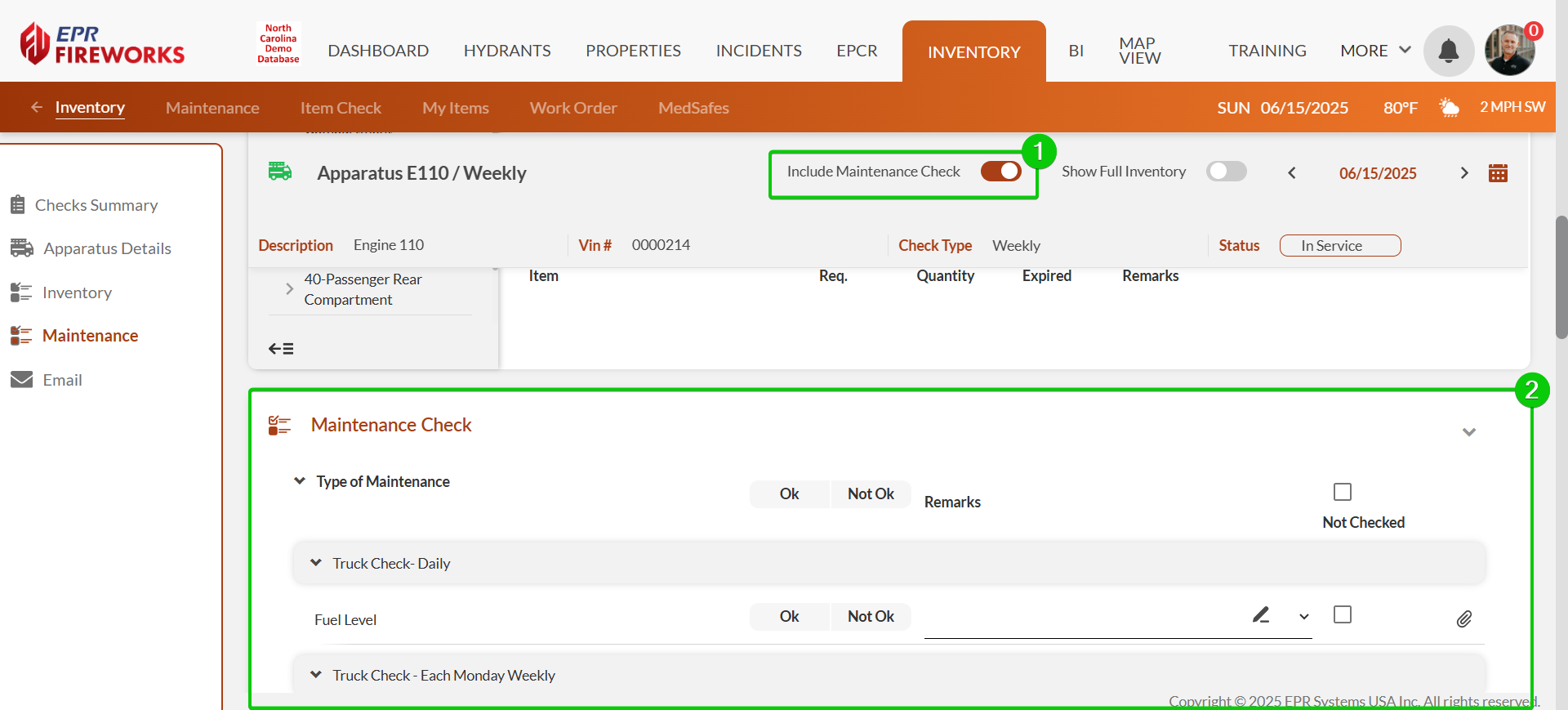
Before You Start
Prerequisites
Maintenance check pages allow you to conduct apparatus and warehouse checks.
Ensure you have appropriate permissions
Use a tablet with a stable internet connection
Clear browser cache if experiencing slowness
Accessing and Verifying Check Details
From the Maintenance list, locate your desired apparatus or warehouse.
Expand the row and select the check type (daily, weekly, monthly, quarterly, bi-annual, annual).
Note: Alternatively, you can select the check type from the Check Summary section within the check page.
Note: See the Check Interface Guide for full information on these sections.
Conducting the Check
Select the type of maintenance check you are checking from the maintenance type tabs.
For each check item, mark according to the condition of the apparatus/warehouse:
OK
Not OK
Not Checked (checkbox on the right)
Note: Selecting OK/Not OK at the top of the list will mark all checks in bulk.
Record apparatus/warehouse check condition:
Add remarks in the Remarks column. Click the pencil icon to select from preset remarks (if configured).
Use the attachments icon to add attachments as needed.
Submitting the Check
Review all entries and notes.
Configure email notifications:
Enable Send Maintenance Check To.
Add recipient email addresses or select mailing lists.
Click Submit [Check Type] Maintenance (button name changes based on check type).
Note: To email the report without submitting it, click Email.
Work Order Integration
When you submit a maintenance check with issues marked as NOT OK, the system automatically opens the New Work Order window. This process is optional and can be skipped.
Creating Work Orders
Mark the issues for the work order.
Note: To mark all issues, select the checkbox above the list.Select the Work Order Internal Status from the dropdown list at the bottom of the window. If no status is selected, the status will default as Open.
Click Create New Work Order.
Note: To submit the check without creating a work order, click Continue Without Creating Work Order.